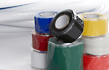 |
硅橡胶自粘带
选用优质进口材料,采用特殊工艺加工制成……
|
|
 |
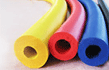 |
硅橡胶管
阻燃硅橡胶管 / 汽车电线硅橡胶管护套管
|
|
 |
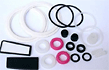 |
硅橡胶模压制品
各种形状均可按照用户要求生产
|
|
 |
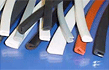 |
硅橡胶密封嵌条
耐热+200度、耐寒-40度、规格形状任提要求
|
|
 |
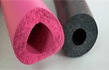 |
硅橡胶海绵制品
各种形状均可按照用户要求生产
|
|
 |
|
 |
新闻资讯 |
|
 |
在硅胶制品广泛应用的当下,硅橡胶自粘带这类轻薄材质产品的市场需求呈现出显著的增长态势。然而,其抗撕裂性能欠佳的问题,已然成为众多使用者面临的突出困扰。采购回来的硅橡胶自粘带在实际使用中易发生撕裂现象,且耐用性不足,这对产品的使用效果与使用寿命均产生了不可忽视的负面影响。深入探究这现象背后的根源,对于提升产品品质、契合市场需求具有意义。 一、原材料及固化过程的影响 硅树脂添加与固化方式:撕裂度作为硅橡胶自粘带制品的一项核心性能指标,原材料硅树脂的添加量以及后续的烘烤固化工艺,对其有着至关重要的影响。以不同的固化方式为例,室温下历经 24 小时固化与在 130℃高温环境下进行烘烤固化,所达成的效果存在明显差异。在室温固化条件下,硅橡胶的分子链交联进程相对迟缓,且存在交联不充分的可能性,这使得材料内部结构在规整性与紧密程度上表现欠佳。研究表明,室温固化后的硅橡胶材料,其内部孔隙率可达 10% - 15%,分子链间的平均间距相较于高温烘烤固化后的状态增大了约 20% - 30% 。而在 130℃的烘烤环境中进行固化,能够显著加速分子链的交联反应,促使材料结构更为致密。不过,这并不表明高温烘烤固化在所有情形下都优于室温固化,关键在于依据硅橡胶的具体配方以及产品的实际需求,精准把控固化条件。倘若固化条件设置不当,例如烘烤温度高于 150℃或者时间超过特定时长,就可能致使硅橡胶分子链过度交联。当分子链交联度超过 80% 时,材料的脆性会显著增加,抗撕裂性能相应下降。 烘烤时间的关键作用:烘烤时间是影响硅橡胶自粘带撕裂度的关键因素之一。时间与温度虽相互独立,但协同作用于硅橡胶的固化成效。在合理的温度区间内,适度延长烘烤时间,有助于硅橡胶分子链充分交联,构建起稳固且坚韧的网络架构。例如,当烘烤温度维持在 130℃ - 140℃时,烘烤时间从原本的 60 分钟延长至 90 分钟,硅橡胶分子链的交联密度可提升约 20% - 30% ,从而有效增强材料的抗撕裂性能。然而,若烘烤时间不足,分子链交联不完全,材料内部便会留存较多的薄弱环节。通过微观结构分析发现,烘烤时间不足的硅橡胶材料,其内部存在大量未充分交联的节点,这些节点在受到外力撕扯时,易成为撕裂的起始点。 二、生产硫化过程的作用 标准生产参数的重要性:硅橡胶自粘带制品厂家在生产硫化过程中,生产参数的设定对产品的抗撕裂强度起着决定性作用。在正常的温度和时间条件下进行硫化,能够确保硅橡胶材料充分反应,进而形成良好的物理性能。根据大量实验数据与生产实践经验,对于一般的硅橡胶自粘带,在 170℃ - 180℃的温度区间内,硫化时长控制在 10 - 15 分钟,能够使产品获得较为理想的抗撕裂性能。在此条件下,产品的撕裂强度可达到 8 - 10kN/m 。但倘若在非正常的加工生产时间以及温度条件下进行硫化,就可能引发一系列问题。 不当操作带来的问题:部分工作人员为追求产量提升,可能会采取一些不当的操作方式,比如提高机台温度以缩短硫化时间。这种方法对于较薄、较小的硅橡胶自粘带产品而言,不仅难以达到预期效果,还会引发诸多负面效应。一方面,过高的温度会使产品硫化速率过快,分子链交联过度。当机台温度超过 200℃时,产品的脆性显著增加,抗撕裂度可降低 30% - 40% 。另一方面,出模过早,产品内部的硫化反应尚未完全结束,即出现产品未完全熟化的现象。此时产品的强度和韧性严重不足,经测试,未完全熟化产品的拉伸强度相较于正常硫化产品降低了 40% - 50%,在受到外力作用时易发生撕裂。因此,在生产过程中,必须严格遵循标准的加工流程,合理调整生产参数,切不可心存侥幸,以免因小失大,对产品质量造成严重影响。 |
|